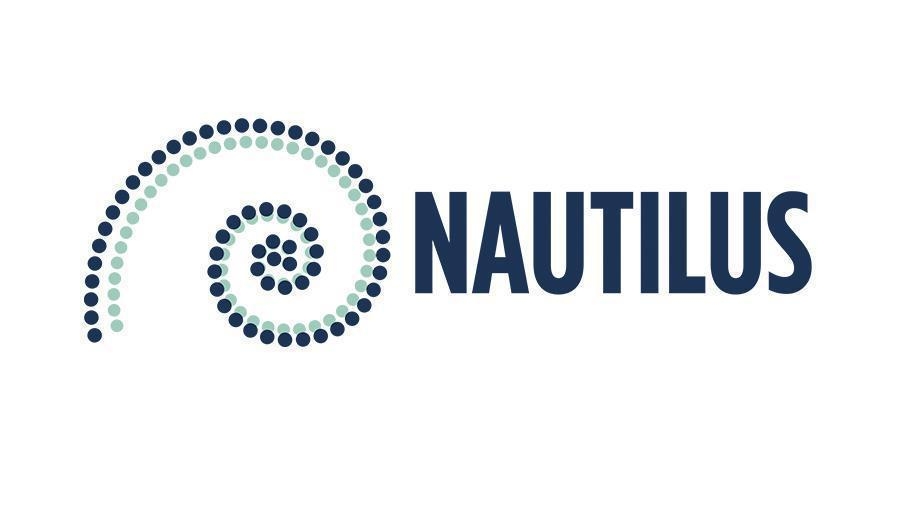
O Porriño, 27 de junio del 2022.- A continuación, se presentan los principales avances conseguidos en la 5ª y última anualidad de NAUTILUS, la Unidad Mixta de Investigación constituida entre Navantia y AIMEN:
- Línea 1A – Celda prototipo para el montaje y punteo de refuerzos en previas y soportes en fase de pre-armamento. Si bien los desarrollos se habían finalizado en la pasada anualidad, en esta última anualidad se procedió a la publicación del artículo “Robotización de operaciones de montaje y soldadura de elementos y estructuras navales” en la revista GMT editado por ACLUNAGA (https://www.aclunaga.es/wp-content/uploads/2022/04/GMT-by-Aclunaga_n%C2%BA9-2.pdf). Dicho artículo resume los trabajos desarrollados en esta línea a lo largo de toda la UMI NAUTILUS y, en particular, en los dos demostradores realizados para el montaje y punteo/soldadura robotizados de elementos como refuerzos de previas y elementos de soportería.
https://youtu.be/SFNTlBjzkz0
https://youtu.be/siJYmeuSDLI
- Línea 2 – Soldadura láser híbrido. Se han efectuado pruebas de soldeo para la monitorización de proceso mediante un sensor IR,forzando la aparición de defectos como faltas de fusión o penetración, típicos en este tipo de uniones soldadas, con el objetivo de evaluar los datos adquiridos por el sensor y poder así establecer una correlación entre las imágenes IR adquiridas durante el proceso y la aparición de los defectos mencionados. Además, se procedió a la realización de pruebas adicionales en uniones de 6mm de espesor con distinta separación entre las chapas con el objetivo de determinar la tolerancia del proceso en cuanto a un posible gap o separación variable, que podría resultar de utilidad en la futura producción. Finalmente se han aplicado los modelos de simulación previamente desarrollados en el proyecto a un panel de dimensiones reales, proporcionado por Navantia, para evaluar virtualmente varias alternativas de soldadura (procesos, anclajes, secuencias, etc.) con el objetivo de parametrizar y optimizar el proceso bajo determinadas condiciones y así reducir la distorsión generada por el proceso de soldeo.
Figura 1. Señal registrada en el sensor MWIR del proceso de soldadura láser híbrido en uniones a tope de 6mm de espesor, 2D (izquierda) y 3D (derecha).
Figura 2. Distorsión obtenida mediante simulación de un panel soldado mediante procesos convencionales (imagen superior) y mediante proceso de soldadura láser híbrido (imagen inferior).
- Línea 3 – Conformado automático de chapas por inducción. Se han realizado pruebas de conformado para obtención de geometría U, tanto en 8 como en 14mm de espesor, para retroalimentar y optimizar el sistema de machine learning. Se ha podido obtener repetibilidad en el conformado. Se ha mejorado también la vida útil del inductor mediante dos vías: 1) garantizando un mayor contacto entre el inductor y el concentrador magnético por medio de una lámina constante de adhesivo; 2) enfriando la superficie del concentrador mediante un ligero soplado durante el proceso de conformado, y esperando tras cada línea de conformado a que la temperatura del concentrador baje de 50ºC.
Figura 3. Celda de conformado mediante inducción electromagnética desarrollada en AIMEN.
- Línea 4 – Soluciones para construcción/reparación naval basadas en composites. Se ha procedido a integración del panel de la puerta fabricado en material composite con los elementos de cierre, marco y contramarco y mamparo. Esta estructura ha sido ensayada a fuego en un centro vasco acreditado según la normativa IMO Code FTP 2010. Apoyándose en la colaboración de la Sociedad de Clasificación Lloyd´s Register, tanto durante la etapa de fabricación de la estructura como en la etapa de ensayo revisando su protocolo y los resultados obtenidos.
Figura 4. Cara no expuesta al fuego durante el ensayo de fuego (izquierda). Cara expuesta al fuego después del ensayo (derecha).
- Línea 5 – Soluciones ligeras para blindaje. Se ha procedido a la realización del ensayo de balística en centro acreditado (Centro La Marañosa, dependiente del INTA-Instituto Nacional de Técnica Aeroespacial) para evaluar así la capacidad de los 4 paneles balísticos fabricados de soportar el impacto del proyectil indicado por la normativa. Tras la realización de los ensayos se puede concluir que se ha superado el Nivel 2 según normativa aplicable (proyectil incendiario, y velocidad de 680 m/s), dado que el proyectil no ha perforado de manera completa los paneles.
Figura 5. Panel balístico multi-material colocado en el bastidor antes del ensayo (izquierda). Probeta tras el ensayo balístico con dos proyectiles (derecha).
- Línea 6 – Soluciones para protección catódica de buques y estructuras offshore. Se procedió a la fabricación de la cabinet, que posteriormente ha sido probada en varios buques de la armada en las instalaciones de NAVANTIA Ferrol, con resultados altamente satisfactorios.
Figura 6. Cabinet desarrollada en el marco de NAUTILUS, durante su testado en fragatas de la serie F-100.
Financiación
La iniciativa NAUTILUS enmarcada en el programa de ayudas para la creación y puesta en marcha de unidades mixtas de investigación, está financiada por la Xunta de Galicia a través de la Axencia Galega de Innovación (GAIN) y cuenta con el apoyo de la Consellería de Economía, Industria e Innovación. A su vez, está cofinanciada con cargo a Fondos FEDER en el marco del eje 1 del programa operativo Feder Galicia 2014-2020. (Ref. IN853A 2018/03).