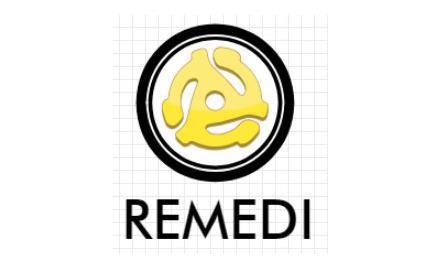
O Porriño, 27 de mayo de 2021.- El principal objetivo del proyecto REMEDI es establecer una metodología de diseño óptima, eficiente y ligera en la fabricación de componentes de tamaño medio/grande, aprovechando al máximo las capacidades de las tecnologías FADDE (Fabricación Aditiva de Deposición Directa) mediante tecnología láser y aportación de polvo metálico.
De esta forma, REMEDI busca superar algunas de las barreras actuales relacionadas con los aspectos de optimización del diseño y productividad en la fabricación digital de componentes de tamaño medio-grande de alto valor añadido, fabricadas mediante tecnologías de deposición metálica por láser, aspectos que impiden una mayor aceptación en la industria de esta tecnología. Así, estos procesos conllevan una cadena de valor conformada por las fases de diseño, configuración de proceso, planificación de proceso, fabricación con control/monitorización en línea, postprocesado, y control de calidad. De todas ellas, para un tipo de tecnología de fabricación basada en la posibilidad de generar formas con mayor grado de libertad, es la fase de rediseño la que realmente ofrece un mayor valor añadido y los beneficios más relevantes. Por tanto, REMEDI se va a enfocar en utilizar esas diferentes etapas de fabricación para retroalimentar el propio diseño, hasta su optimización más eficiente.
En base a esta necesidad industrial para esta tecnología emergente, el objetivo de REMEDI es precisamente establecer la metodología de diseño para procesos de Laser Metal Deposition (LMD) con la intención de disminuir las consecuencias significativas del diseño en la calidad final de la pieza.
Para implementar el concepto de Quality-by-Design (QBD) en la fabricación de los prototipos del proyecto, se utilizará una plataforma software/hardware que consistirá en:
- Una unidad de ingeniería fuera de línea (offline engineering unit), que integra bajo la misma capa diferentes tecnologías CAx comerciales y,
- Una instalación física de fabricación aditiva por LMD, para implementar una metodología de Calidad por Diseño y validarla para la fabricación aditiva de componentes de gran tamaño optimizados para conseguir cero defectos.
Concretamente, este entorno se implementará en dos instalaciones de fabricación (una fábrica española, Smarmec y una fábrica turca, Coskunoz R&D), para demostrar el concepto y obtener la capacidad de reproducibilidad futura en cualquier industria demandante. La tecnología REMEDI se validará para dos sectores diferentes demandantes de componentes de alto valor añadido: aplicaciones espaciales y componentes de aeronaves.
Los objetivos planteados se alcanzarán mediante la consecución de los siguientes hitos tecnológicos:
- Realizar una optimización topológica del diseño de la pieza basada en los requisitos de integridad estructural y las cargas funcionales, para proporcionar un componente más eficiente en términos de uso de materia prima, coste de producción y tiempo de entrega.
- Determinar las capacidades de fabricabilidad del proceso LMD en sus diferentes configuraciones de parámetros de equipo/parámetros de proceso, con el fin de alimentar la herramienta de Optimización Topológica con datos de escenarios industriales reales.
- Actuar sobre el ciclo configuración de sistema/estrategias de deposición/simulación multifísica para alcanzar un equilibrio térmico, que sirva al mismo tiempo para evaluar automáticamente el diseño de la pieza obtenido en los pasos anteriores, detectando zonas de la pieza que puedan ser conflictivas para su fabricación o para la funcionalidad final de la pieza.
- Analizar los datos vinculados a la potencia láser y la temperatura del baño fundido en cualquier punto de la trayectoria de proceso mediante sistemas de monitorización, para vincularlos a la etapa de diseño y proponer nuevos cambios de diseño en base a esto.
Consorcio REMEDI
Para afrontar este ambicioso reto, se ha consolidado un consorcio nacional multidisciplinar compuesto por 3 empresas, con las capacidades y el conocimiento necesario para cubrir toda la cadena de valor del proyecto:
CT INGENIEROS, proporciona servicios de ingeniería para una amplia gama de actividades desde las etapas de diseño de productos a las actividades de ingeniería y procesos de mantenimiento en diferentes sectores: aeronáutica, ferrocarril, automoción,naval, energías renovables y plantas industriales (Diseño de producto, Ingeniería de Fabricación, Herramientas de diseño y cálculo o Ingeniería de Calidad, entre otros aspectos).
RAMEM, como PYME dedicada al diseño, fabricación y montaje de equipos mecánicos y electromecánicos, principalmente para la industria aeronáutica y aeroespacial.Para estas aplicaciones, ofrece servicios que recorren toda la cadena de valor,desde la fase de diseño, la ingeniería de fabricación o el desarrollo de ensayos y control de calidad.
SMARMEC, spin- off de la empresa Tecnichapa, que ofrece soluciones integrales a sus clientes en el sector de la calderería fina y de precisión. En el ámbito de REMEDI, es de vital importancia su experiencia en el desarrollo de soluciones y fabricación para prototipos y series cortas de componentes de alto valor añadido.
El consorcio cuenta con el apoyo de AIMEN Centro Tecnológico, entidad con amplia experiencia en el desarrollo de tecnologías láser, en el desarrollo y puesta a punto de procesos de fabricación aditiva y en el desarrollo de soluciones de monitorización y control para los mismos.
A mayores, a nivel europeo el consorcio se completa con los socios turcos Coşkunöz R&D y TAI (Turkish Aerospace Industries).
Presupuesto y financiación
El proyecto REMEDI, tiene una duración de 30 meses (está previsto que finalice en el 2021) y cuenta con un presupuesto aproximado de 2M€. El proyecto internacional ha sido aprobado bajo la convocatoria SMART EUREKA Advanced Manufacturing. A nivel nacional, el proyecto está subvencionado por el CDTI a través del programa INNOGLOBAL 2018, y apoyado por el Ministerio de Ciencia, Innovación y Universidades con un presupuesto total de 1.335.516,00€, y una ayuda total de 392.657,00€.
A Project funded under the SMART EUREKA CLUSTER on Advanced Manufacturing programme.