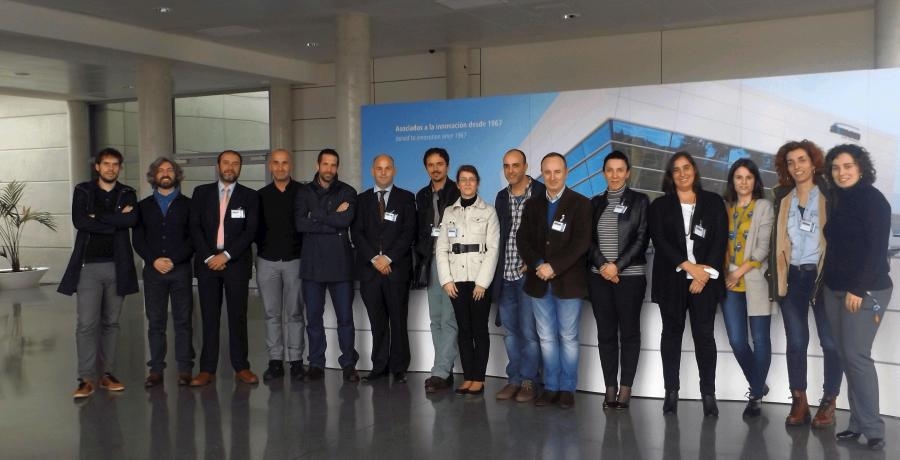
El proyecto FADO, enmarcado en el Programa FEDER-INNTERCONECTA, está liderado por CT Ingenieros y en él participan, además de AIMEN, las empresas Hydracorte, Airgrup, Syspro, Unimate y la Universidad de A Coruña.
Con él se conseguirá la fabricación aditiva mediante láser de piezas de grandes dimensiones, de hasta 5 metros, mejorando la calidad del producto final y aumentando la rentabilidad.
En la industria aeronáutica se podrá emplear para la fabricación de piezas en aleaciones ligeras de gran tamaño; mientras que en los sectores de automoción y metalmecánico permitirá la producción de componentes estructurales de grandes dimensiones. Asimismo, el sistema contribuirá a fabricar piezas de alto valor añadido para la industria energética, petroquímica o naval.
24 de febrero de 2016, O Porriño.- AIMEN Centro Tecnológico participa en el desarrollo de un innovador sistema robotizado de fabricación aditiva por láser, que permitirá la reparación y fabricación de componentes de grandes dimensiones para los sectores aeronáutico, automoción, metalmecánico o naval, entre otros. Se trata del proyecto FADO, que lidera CT Ingenieros, y en el que también participan las empresas gallegas Hydracorte, Syspro y Unimate, la andaluza Airgrup; además de AIMEN y la Universidad de A Coruña.
Este sistema robotizado combinará el aporte láser de hilo y polvo. El dispositivo constará de un cabezal híbrido que garantizará la flexibilidad, productividad y robustez necesaria para añadir uno u otro material en función de los requisitos de precisión de la pieza. Gracias a esta solución, que será validada industrialmente sobre componentes prototipo de aluminio para el sector aeronáutico, se pretende mejorar el ratio “Buy-to-Fly”, es decir, la eficiencia del material final empleado, en más de un 30%.
Asimismo, se ahorrará una significativa cantidad de material, al potenciar el uso de aporte de hilo frente al de polvo, una tecnología más limpia y respetuosa con el medio ambiente que, además, implica una reducción de costes. Otros de los beneficios derivados de este innovador sistema es la disminución de la cantidad de residuos que genera, en comparación de procesos sustractivos habituales; y la mejora de la productividad, al conseguir mayores tasas de deposición del material (respecto a los sistemas de deposición exclusivos de polvo) y una mayor velocidad del proceso.
Las aplicaciones industriales del proyecto son diversas. En la industria aeronáutica, se podrá emplear para la fabricación de piezas en aleaciones ligeras de gran tamaño; mientras que en los sectores de automoción y metalmecánico, permitirá la producción de componentes estructurales de grandes dimensiones. Asimismo, el sistema contribuirá a fabricar piezas de alto valor añadido para la industria energética, petroquímica o naval.